In the electronic Granulator In the 1970s, it was widely used in Europe. In China, the social and economic system and market were relatively closed at that time, so it was impossible to see such a "magic weapon". At that time, the basic method of counting medicine granules, candy granules and granules in China was still the way of counting tablets and counting granules by hand, which was very simple and unhygienic.
In Europe at that time, the real starting point of using this electronic granulator was to solve the fatigue of workers, not to reduce labor, reduce costs and other "noble scientific research themes". So the embryonic development of the electronic granulator at that time was a small electronic granulator.
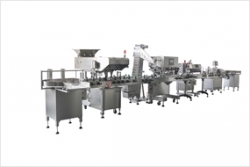
Early generation electronic granulator:
It is a small electronic grain counting machine, and its volume is only the size of a desktop computer. It can also be said that it is an electronic instrument. It mainly applies the principle of photoelectric grain counting sensor and is used for counting small moving objects. Due to its advantages of high speed, non-contact measurement, and low requirements for the location of falling objects, it is widely used in seed counting machines in agricultural instruments.
Second generation Photoelectric granulator :
It was not formally applied to the pharmaceutical industry until the end of the 1970s. We call it the early generation of photoelectric granulator. Maybe I prefer to call it the automatic electronic granulator. Why do you say that? Because it is developed and innovated on the basis of the original number of seeds, the real meaning is a leap in the number of high-speed seeds. It is a practical solution to the labor force, reduce the use cost, and fully realize the full automation of the outsourced mechanical packaging equipment in the pharmaceutical industry.
At that time, the technical working principle: through initial adjustment of the vibrating feeding plate, the particles in the hopper vibrate continuously along the track of the vibrating plate until they fall down from the front photoelectric detection channel and touch the photoelectric sensor to start working and counting. When the particles reach the predetermined quantity, the PLC signals the electric valve to close the feeding port, and the counted particles fall on the bottle at the outlet, To realize the function of counting particles (many domestic manufacturers of counting particles also basically use this form to complete), the mechanical part is controlled by servo motor and cylinder, This method is widely used in the pharmaceutical industry.
Disadvantages: The error rate and speed of this method are not good. Because the single PLC is used to execute commands in serial, the speed cannot be fast, and the infrared pulse is scanned in a single line. The implementation of the photoelectric granulator in a real sense is due to the fact that in recent years, the labor cost has risen several times, and the pharmaceutical factory has again put forward higher requirements for the counting capacity of the granulator. There are also two core points: the speed of the granulator should be faster and the accuracy should be higher.
The third generation photoelectric (3D) granulator
With the promotion of customers' application requirements, the real photoelectric granulator was born in 2009, and it is also a granulator with good customer satisfaction and application up to now. So what is the difference between this photoelectric (3D) granulator and the previous photoelectric granulator?
1: The software system for counting grains should be changed to FPGA, which is also a popular software system currently used in aviation technology. Advanced features are radiation resistance, high performance and low power consumption
FPGA can reconstruct the structure and working mode of the hardware through software programming. Modifying the software program is equivalent to changing the hardware, which is fast and reliable. Practice has proved that FPGA software system has the following advantages:
1. It can realize parallel work on hardware, and has broad prospects in real-time measurement and control and high-speed applications;
2. FPGA device is realized by software in function development, but its physical mechanism is as reliable as pure hardware circuit
3. The high reliability of FPGA just overcomes the problem that other manufacturers are congenitally deficient in running out of MCU, and the accuracy of several chips is not high. As well as the use of a single PLC, the serial execution of instructions is not fast. It introduces the mature high-speed electronic digital chip technology of well-known manufacturers in Taiwan, and the operating system based on FPGA high-speed microprocessor technology and full Chinese dynamic graphic display. The parameters can be set or adjusted on.
4. Automatic fault diagnosis and real-time monitoring alarm display system, and can store multiple groups of parameters, which can be called directly when changing products.