How to reduce dust Granulator What is the processing impact of?
The granulator is widely used in the pharmaceutical and food industries, and is one of the key equipment in the production line of granular medicine cans. It works by oscillating blanking and uses photoelectric effect. Although it is not constrained by the numbering template, it can handle various shapes and specifications. When counting dusty articles such as tablets and pills, the problem of inaccurate counting will occur for a long time. So how should we deal with this problem?
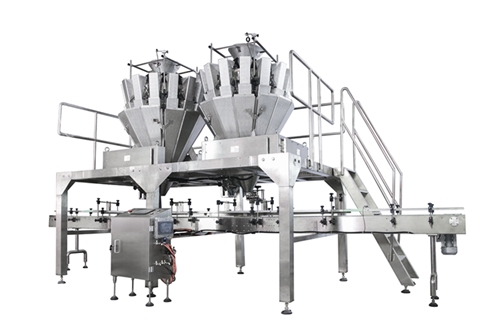
The traditional granulator adopts multi-channel transportation method, which arranges the items in each channel into a row, and triggers the corresponding photoelectric sensor to count when falling. When the cumulative quantity of each channel reaches the guideline value, the independent gate below the sensor will be closed in sequence, so that the cargo logistics can stack according to the guideline quantity. However, the problem with this counting method is that:
1. The photoelectric sensor needs to work close to the material, and its sensitivity is simply affected by the dust generated by the material.
2. The sensor array is required to cover the width of the channel. There is a certain distance between sensors, and small objects have a certain probability of detecting blind spots.
3. The resolution of array sensor is limited, so it can not effectively identify debris and sundries.
4. Multi stage oscillating disk is used to disperse materials into multiple rows and separate them, occupying large plane space.
5. The channel gate requires very high response speed, and the cleanliness of compressed air is very high. A slight delay in door response may damage objects or cause inaccurate stacking.
Each channel of the granulator can only allow one item to pass through. If the passage is too small, it is not suitable for larger items. If the channel is too large, the device volume will be added proportionally. When blind spots are detected, the universality of the device will be constrained.
1. Visual counting method, remote imaging, not affected by dust.
2. High resolution, suitable for objects of different sizes, no blind spot.
3. It can distinguish sundries and broken particles, eliminate small piles of materials, and prevent production capacity waste.
4. The single-layer tray feeding is integrated with the channel, greatly improving the feeding density and production capacity.
5. No high-speed gate is required to prevent the risk of gate fragmentation, and there is no requirement for the cleanliness of compressed air.
6. Small size, optimal capacity/floor area ratio, convenient for production line layout.